Introduction
Manufactured sand (M-sand) has emerged as a sustainable alternative to natural sand due to the depletion of natural sand resources. Various types of rocks and industrial waste can be used to produce M-sand, making it a cost-effective and environmentally friendly solution for construction. This guide explores suitable materials, production processes, and essential equipment for manufacturing high-quality sand.
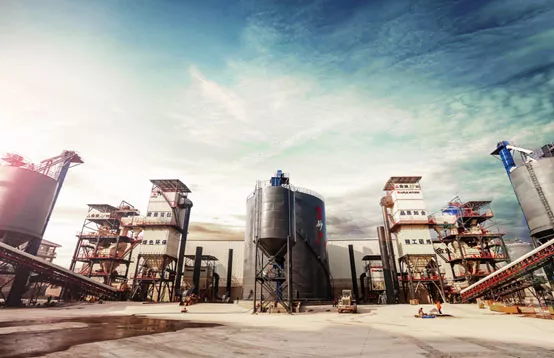
Common Raw Materials for M-Sand Production
Several raw materials are commonly used in manufactured sand production:
1. Hard Rock Aggregates
- River Pebbles
- Basalt
- Granite
- Limestone
- Bluestone
- Iron Ore
These materials are durable, making them ideal for use in construction and concrete production. For instance, basalt sand enhances concrete strength and insulation properties, making it a preferred choice for high-rise buildings.
2. Sandstone and Quartzite
- Sandstone is a sedimentary rock rich in quartz and feldspar, known for its high durability and excellent grain shape, making it a perfect raw material for M-sand.
- Quartzite, with its resistance to weathering and moisture, is often used in decorative construction materials.
3. Tailings, Slag, and Construction Waste
- Industrial waste materials such as mine tailings and steel slag can be repurposed for M-sand production.
- Demolition waste, including concrete blocks and bricks, can also be crushed and processed into reusable aggregate.
Key Considerations for Selecting Raw Materials
To ensure high-quality M-sand production, the following factors should be considered:
- Compressive strength: Raw materials should have a minimum strength of 80 MPa.
- Chemical stability: Materials should be free from excessive acids or alkalis.
- Minimal impurities: High clay or mud content affects sand quality and should be avoided.
M-Sand Production Process
The production process varies depending on the raw material type and production capacity. Below are two common production setups:
1. High-Capacity Production (Above 200 TPH)
Equipment Used:
- Vibrating Feeder
- Jaw Crusher (Primary Crushing)
- Cone Crusher (Secondary Crushing)
- Impact Crusher (Tertiary Crushing)
- Vibrating Screen
- Sand Washer
- Belt Conveyor
This setup is ideal for hard materials, providing high output and uniform grain shape. Impact crushers are used to refine the material by reducing flaky particles and ensuring a better shape for construction applications.
2. Low-Capacity Production (Below 200 TPH)
Equipment Used:
- Vibrating Feeder
- Jaw Crusher
- Roll Crusher or Double-Stage Crusher
- Vibrating Screen
- Belt Conveyor
This method is suitable for smaller stone processing plants that require cost-effective and energy-efficient equipment.
The Growing Demand for M-Sand
With rising construction costs and limited availability of natural sand, manufactured sand has become an essential alternative. It is widely accepted in infrastructure projects such as:
- Road construction
- High-rise buildings
- Concrete production
Benefits of Using M-Sand
✔ Sustainable alternative to natural sand ✔ Consistent quality and grain shape ✔ Cost-effective and easily accessible
Manufactured sand is revolutionizing the construction industry, offering a sustainable and high-performance alternative to natural sand. By choosing the right raw materials and production equipment, businesses can enhance efficiency and reduce costs. Explore the best crushing solutions for your M-sand production needs today!