Crushers for High-Hardness Stones: Unleashing Efficiency with DAINAMU Solutions
Introduction: The Power of Crushers in Stone Processing
In industries like construction, mining, and infrastructure development, stone crushing is a cornerstone process that transforms raw, oversized rocks into usable aggregates such as gravel, sand, and crushed stone. However, processing high-hardness stones—like granite, basalt, andesite, and river pebbles—presents unique challenges. These materials are renowned for their toughness, abrasiveness, and resistance to breaking, demanding robust and efficient crushing equipment to achieve optimal results.
This is where DAINAMU, a trusted name in the industry, steps in. Offering cutting-edge crusher solutions, DAINAMU specializes in equipment designed to tackle the toughest stones while ensuring high productivity and durability. Whether you’re breaking down granite for road bases or producing sand from river pebbles, DAINAMU’s advanced technology provides the reliability and performance you need. In this article, we’ll explore how crushers excel in the crushing and screening of high-hardness stones, diving into their types, applications, technical specifications, and real-world success stories.
For more details on DAINAMU’s offerings, check out their crusher lineup.
Types of Crushers and Their Working Principles
To process high-hardness stones effectively, selecting the right crusher is critical. Below, we outline the primary types of crushers and their roles in handling tough materials like granite, basalt, and river pebbles.
Jaw Crushers: The Primary Workhorse
Jaw crushers are the go-to choice for primary crushing, designed to handle large, high-hardness stones with ease. They work by compressing material between a fixed and a movable jaw, reducing large rocks into smaller, manageable sizes. Their rugged construction makes them ideal for breaking down granite and basalt in quarries.
- Key Advantage: High crushing ratio and durability.
- Application: Initial crushing of oversized hard rock.
Explore DAINAMU’s jaw crushers for robust primary crushing solutions.
Cone Crushers: Precision in Secondary Crushing
For finer reduction, cone crushers take the stage. These machines use a rotating cone to crush stones against a fixed wall, producing uniform aggregates. They’re highly effective for basalt and andesite, offering excellent particle shape and high throughput.
- Key Advantage: Superior output consistency.
- Application: Secondary crushing of high-hardness stones.
Learn more about DAINAMU’s cone crushers.
Impact Crushers: Versatile Fine Crushing
Impact crushers utilize high-speed rotors to strike materials, making them suitable for medium-hardness stones and producing high-quality aggregates. While they excel with river pebbles, they’re often paired with other crushers for tougher rocks like granite.
- Key Advantage: Excellent cubical shape output.
- Application: Fine crushing and shaping.
Vertical Shaft Impact (VSI) Crushers: Sand-Making Masters
VSI crushers are specialized for producing artificial sand from river pebbles and other stones. They use a high-speed rotor to throw materials against anvils, creating finely crushed particles ideal for concrete production.
- Key Advantage: Precision in sand production.
- Application: Final-stage crushing for artificial sand.
Discover DAINAMU’s VSI crushers.
Applications of Crushers in High-Hardness Stone Processing
High-hardness stones require tailored crushing and screening processes to maximize efficiency and output quality. Here’s how different crushers shine with specific materials:
Granite: Tough and Durable
Granite, a popular choice for construction aggregates, demands a combination of jaw crushers for primary breaking and cone crushers for secondary refinement. Its high compressive strength (up to 200 MPa) necessitates durable equipment like those from DAINAMU.
- Process: Jaw crusher → Cone crusher → Screening.
- Output: Coarse aggregates for roads and buildings.
Basalt: Abrasive and Dense
Basalt, known for its wear-inducing properties, benefits from cone crushers in secondary stages after initial jaw crushing. Its density makes it ideal for high-strength concrete.
- Process: Jaw crusher → Cone crusher → Impact crusher (optional).
- Output: Fine aggregates and ballast.
Andesite: Hard and Versatile
Andesite shares similarities with basalt but often requires VSI crushers for final shaping due to its use in decorative aggregates.
- Process: Multi-stage crushing with screening.
- Output: Polished stones and sand.
River Pebbles: Smooth Yet Challenging
River pebbles, with their rounded surfaces, are perfect for impact crushers and VSI crushers, producing high-quality sand for construction.
- Process: Impact crusher → VSI crusher → Screening.
- Output: Artificial sand and gravel.
Technical Specifications: Comparing Crusher Performance
To illustrate the capabilities of crushers for high-hardness stones, here’s a comparison table:
Crusher Type | Max Feed Size (mm) | Capacity (t/h) | Power (kW) | Best For |
---|---|---|---|---|
Jaw Crusher | 1200 | 50-1000 | 55-200 | Granite, Basalt |
Cone Crusher | 350 | 100-500 | 75-315 | Basalt, Andesite |
Impact Crusher | 500 | 50-300 | 55-250 | River Pebbles |
VSI Crusher | 60 | 100-600 | 110-400 | Artificial Sand |
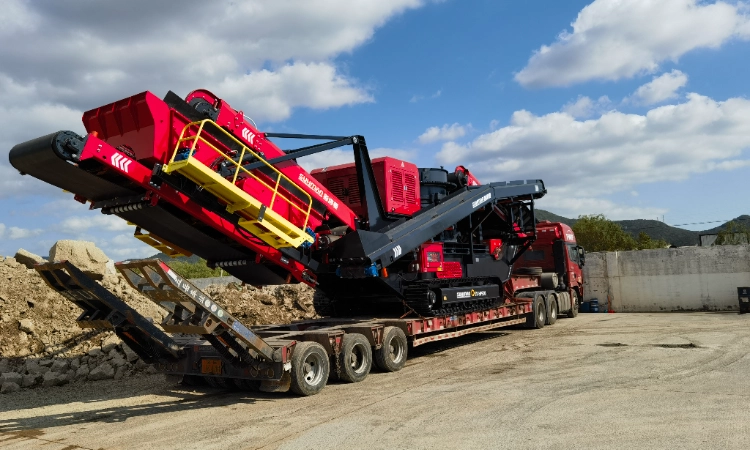
This table highlights how DAINAMU’s equipment meets diverse project needs. For detailed specs, visit https://dainamu.com/products/.
Real-World Applications: DAINAMU in Action
Case Study 1: Granite Quarry in Southeast Asia
A quarry processing granite for highway construction adopted DAINAMU’s jaw crusher and cone crusher combo. The result? A 30% increase in output and reduced maintenance costs due to the equipment’s wear-resistant design.
Case Study 2: River Pebble Sand Plant
In a sand production facility, DAINAMU’s VSI crusher transformed river pebbles into premium sand, meeting strict concrete standards and boosting profitability.
Conclusion: The Future of Stone Crushing
Crushers are indispensable for processing high-hardness stones, and DAINAMU stands at the forefront with innovative, reliable solutions. From granite to river pebbles, their equipment ensures efficiency, quality, and sustainability. As technology advances, expect smarter, energy-efficient crushing systems to redefine the industry.