In the aggregates, mining, and construction industries, selecting the right equipment is critical for operational efficiency, cost management, and product quality. This analysis compares three key pieces of equipment: the Mobile Crushing Plant, the Mobile Screening Plant, and the Dual-core Jaw Crusher. Each serves distinct yet complementary roles in material processing, and understanding their differences is essential for informed purchasing or operational decisions in 2025.
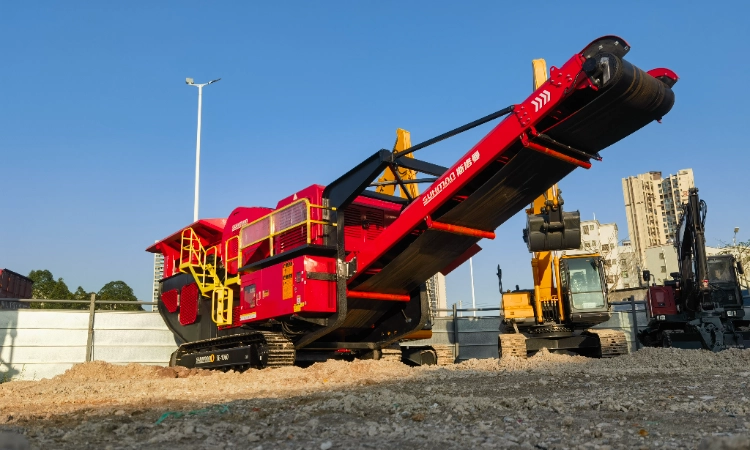
Overview of Each Equipment Type
- Mobile Crushing Plant
A mobile crushing plant is an integrated, portable system designed to crush materials such as rock, concrete, or asphalt into smaller sizes. It typically includes a primary crusher (e.g., jaw or impact), feeder, conveyors, and sometimes a screening unit, all mounted on a wheeled or tracked chassis. Renowned manufacturers like Terex Finlay and Kleemann emphasize their versatility and rapid deployment for on-site processing. - Mobile Screening Plant
A mobile screening plant focuses on separating crushed materials into specific size fractions. Equipped with vibrating screens, it sorts aggregates for further processing or final use, often working in tandem with crushing plants. Companies like Powerscreen highlight their high-throughput screening capabilities and mobility, ideal for quarries and recycling operations. - Dual-core Jaw Crusher
Assuming this refers to an advanced jaw crusher (e.g., dual-power or hybrid models), the dual-core jaw crusher is a specialized primary crusher designed for superior performance. It features a robust jaw mechanism, often with hybrid diesel-electric power options, as seen in models like Sandvik’s QJ341+ or Metso’s Lokotrack LT120E. It excels at reducing hard materials with precision and efficiency.
Detailed Comparison
The following table provides a side-by-side comparison based on key technical and operational parameters:
Parameter | Mobile Crushing Plant | Mobile Screening Plant | Dual-core Jaw Crusher |
---|---|---|---|
Primary Function | Crushes large materials into smaller sizes | Screens and sorts materials into size fractions | Crushes hard materials with high efficiency |
Core Component | Jaw, impact, or cone crusher | Vibrating screen (single or multi-deck) | Advanced jaw crusher (e.g., dual-power) |
Mobility | Tracked or wheeled chassis | Tracked or wheeled chassis | Typically part of a mobile plant or standalone |
Capacity (tons/hour) | 100–800 (varies by model, e.g., Terex J-1170) | 200–1000 (e.g., Powerscreen Chieftain 2100X) | 200–600 (e.g., Sandvik QJ341+) |
Material Input | Large rocks, concrete, asphalt | Pre-crushed aggregates | Hard rock, ore, demolition waste |
Output Product | Coarse to medium aggregates | Sized aggregates (e.g., 0-5 mm, 5-20 mm) | Coarse aggregates (adjustable) |
Power Options | Diesel, electric, or hybrid | Diesel or electric | Diesel-electric hybrid (common in dual-core) |
Typical Application | Quarrying, recycling, construction | Aggregate production, recycling | Mining, quarrying, heavy-duty crushing |
Integration | Often includes screening | Works with crushing plants | Standalone or part of crushing plant |
Setup Time | 30–60 minutes | 15–30 minutes | 30–45 minutes (if mobile-mounted) |
Cost Range (USD) | $150,000–$1,000,000 | $100,000–$500,000 | $200,000–$700,000 |
Maintenance Complexity | Moderate (crusher wear parts, conveyors) | Low (screen mesh, bearings) | High (jaw plates, hybrid systems) |
Leading Manufacturers | Metso, Kleemann, Terex Finlay | Powerscreen, McCloskey, Sandvik | Sandvik, Metso, Keestrack |
In-Depth Analysis
- Purpose and Functionality
- Mobile Crushing Plant: Designed for primary or secondary crushing, it reduces raw materials into manageable sizes. For example, Kleemann’s MOBICAT MC 110 Zi EVO handles up to 330 tons/hour, ideal for quarry operations.
- Mobile Screening Plant: Focused on grading, it ensures product consistency. The Powerscreen Warrior 1400X, with a capacity of 400 tons/hour, excels at separating fine sands from coarse gravel.
- Dual-core Jaw Crusher: Built for heavy-duty primary crushing, it offers precision and durability. Sandvik’s QJ341+ features a pre-screen and double-deck system, boosting throughput by up to 600 tons/hour.
- Mobility and Deployment
All three are mobile, but their deployment differs. Crushing and screening plants are full systems requiring coordinated setup, while a dual-core jaw crusher (if standalone) focuses solely on crushing, potentially simplifying logistics. Tracked versions, common across all, dominate in rough terrain, as noted by Astec Industries. - Capacity and Efficiency
- Crushing plants vary widely in capacity, balancing crushing and conveying.
- Screening plants prioritize throughput, often exceeding crushing plants in tons/hour due to simpler mechanics.
- Dual-core jaw crushers, with advanced designs, optimize energy use and output, reducing downstream processing needs.
- Applications and Synergy
These units often work together. A mobile crushing plant breaks down material, a dual-core jaw crusher handles the toughest inputs, and a screening plant refines the output. For instance, in a quarry, the jaw crusher processes blasted rock, the crushing plant manages secondary reduction, and the screening plant sorts the final product. - Cost and Maintenance
- Crushing plants are the priciest due to their complexity, with higher maintenance needs for multiple components.
- Screening plants are more affordable and simpler to maintain, focusing on screen mesh replacement.
- Dual-core jaw crushers, with hybrid systems, demand skilled upkeep but offer long-term savings via efficiency.
Authoritative Insights
Industry leaders like Metso and Sandvik report that mobile solutions dominate modern operations due to their flexibility and reduced haulage costs. A 2024 study by Construction Equipment Magazine highlights a 15% rise in mobile plant adoption, driven by infrastructure projects globally. For dual-core designs, Sandvik’s hybrid technology claims up to 30% fuel savings over traditional diesel models, a trend shaping 2025 purchases.
Conclusion
Choosing between a Mobile Crushing Plant, Mobile Screening Plant, and Dual-core Jaw Crusher depends on your operational goals. Need raw material reduction? Opt for the crushing plant or jaw crusher. Prioritizing graded aggregates? The screening plant is your match. For heavy-duty, efficient crushing, the dual-core jaw excels. Together, they form a robust processing chain—select based on your site, budget, and output needs.